Reignite Combustion Efficiency:
Reignite Combustion Efficiency: How the SAS Patented In-Line Diffuser Solves the Coal Ribboning Crisis in Low NOx Burners
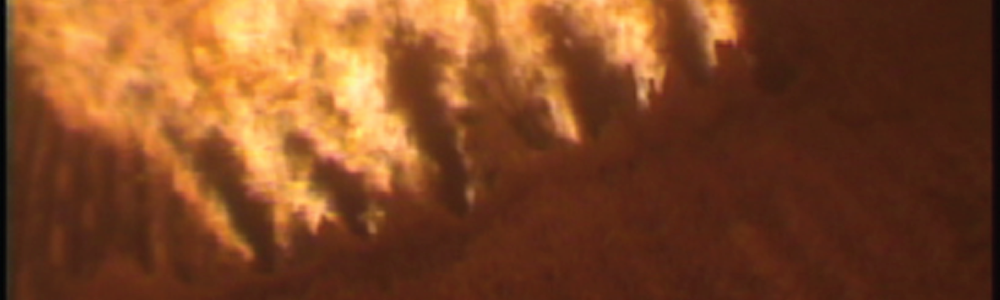
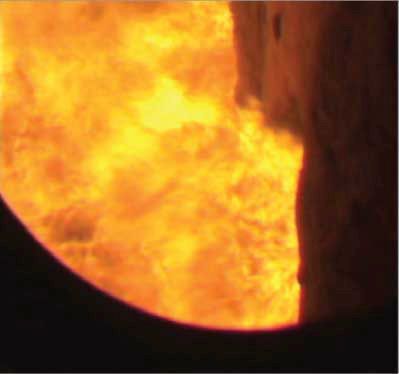
In the quest to reduce NOx emissions and improve combustion efficiency, Low NOx burners have long been hailed as a solution. But what if the very conditions inside your fuel piping are sabotaging their performance?
Welcome to the hidden challenge of coal ribboning—and the patented technology that finally solves it: the SAS Global In-Line Diffuser.
The Problem: Is Your Low NOx Burner Really Performing?
Modern coal-fired power plants rely on specific, pre-engineered stoichiometric air-to-fuel ratios to achieve optimal combustion and reduced NOx formation. Low NOx burners are designed to operate within, often unobtainable or inconsistent, air-to-fuel ranges to stage combustion, suppress peak flame temperatures, and limit nitrogen oxide formation.
But there’s a catch...
At the inlet to every burner is an elbow, or scroll; a design that inadvertently creates segregated strands of coal and air, better known as
“coal ribbons.” This phenomenon causes wild variations in the air/fuel ratio across the burner face:
- Too much air: Leads to premature ignition, high NOx, and damage to burner tips.
- Too much coal: Leads to delayed combustion, slagging, unburned carbon (LOI), and wasted heat.
These uneven flow conditions violate the very principle Low NOx burners rely on a homogeneous fuel/air mixture. The result? Poor combustion stability, higher emissions, costly maintenance, and diminished heat rate performance.
The SAS Global Solution: Patented In-Line Diffuser Technology
The SAS Patented In-Line Diffuser is engineered to
disrupt coal ribboning just upstream of the burner tip. Its job is simple but powerful: force the mixture of coal and air into a
uniform, homogeneous flow profile before entering the boiler.
With a consistent fuel-to-air mixture:
- Combustion begins at the intended location—not prematurely or too far down the flame path.
- Burner tips are protected from localized wear and overheating.
- NOx reduction strategies (like secondary and over-fire air) become more effective.
- The boiler heat rate improves, and so does fuel efficiency.
Proof in the Flame: Before & After Performance:
WALL FIRED BURNER EXAMPLE
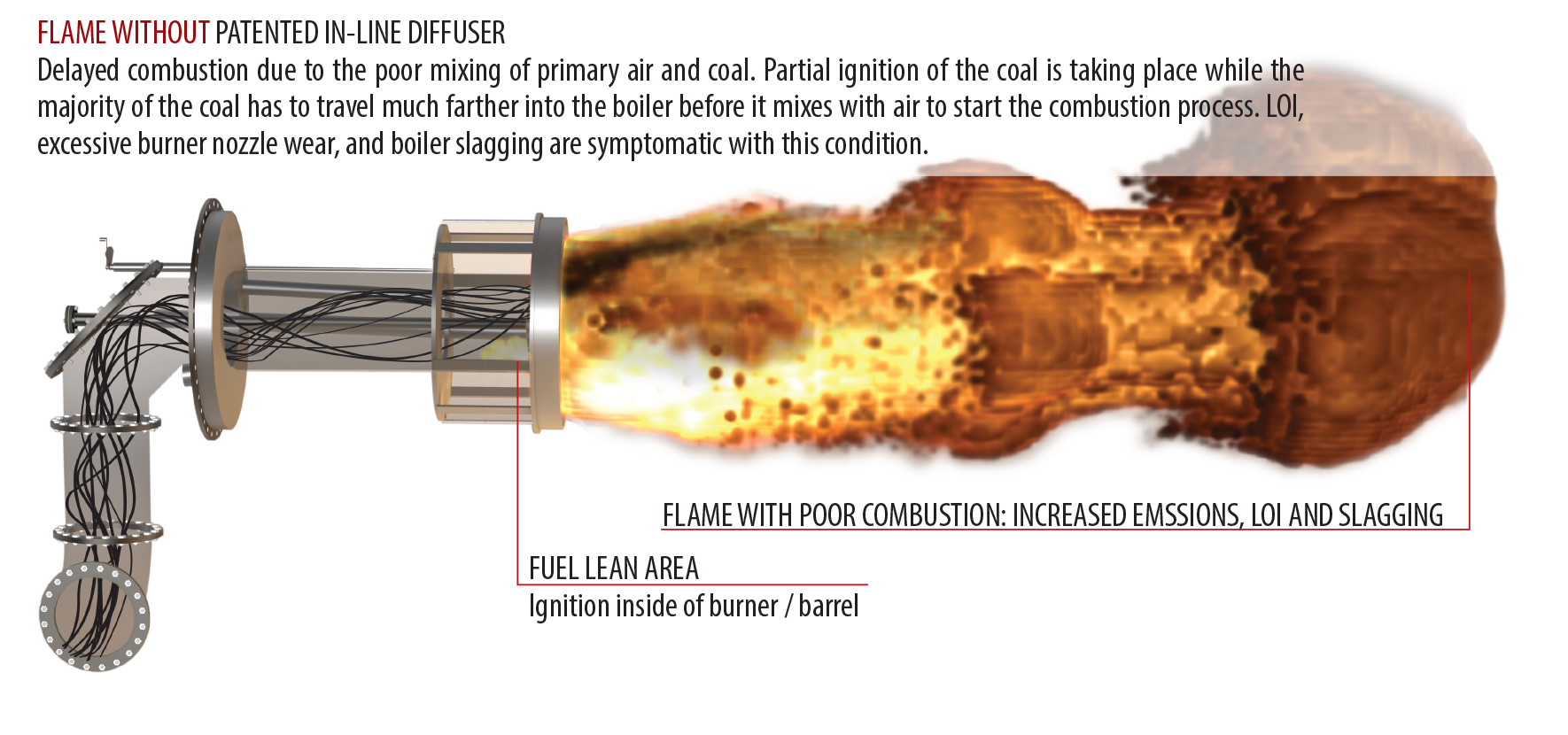
Wall-Fired Burners – Without Diffuser:
- Delayed ignition due to poor mixing
- High LOI
- Slagging and hot spots
- Burners degrade prematurely
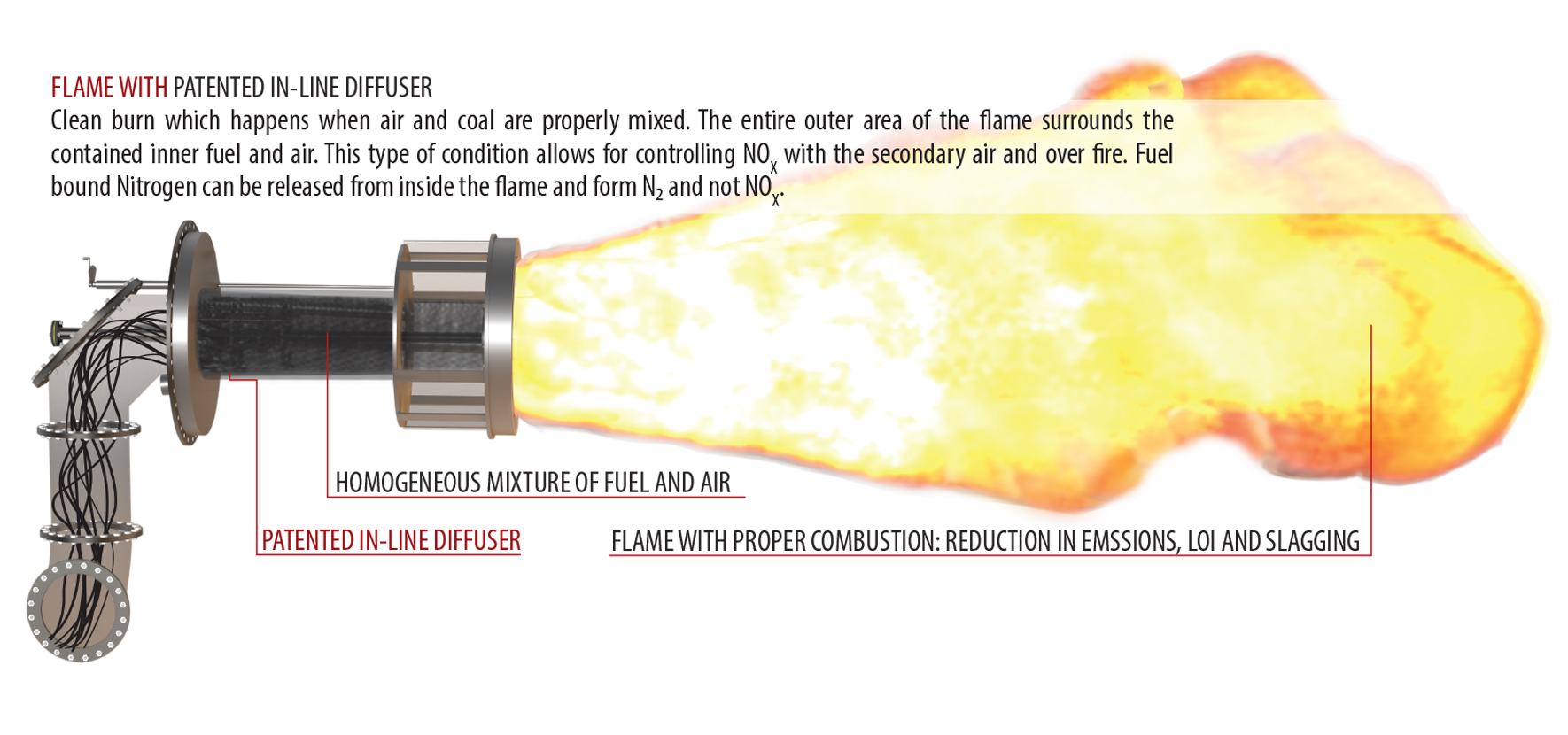
Wall-Fired Burners – With Diffuser:
- Early, controlled ignition
- Uniform flame envelope
- Efficient fuel burnout
- NOx controlled with secondary air—not excessive burner modifications
CORNER FIRED BURNER EXAMPLE
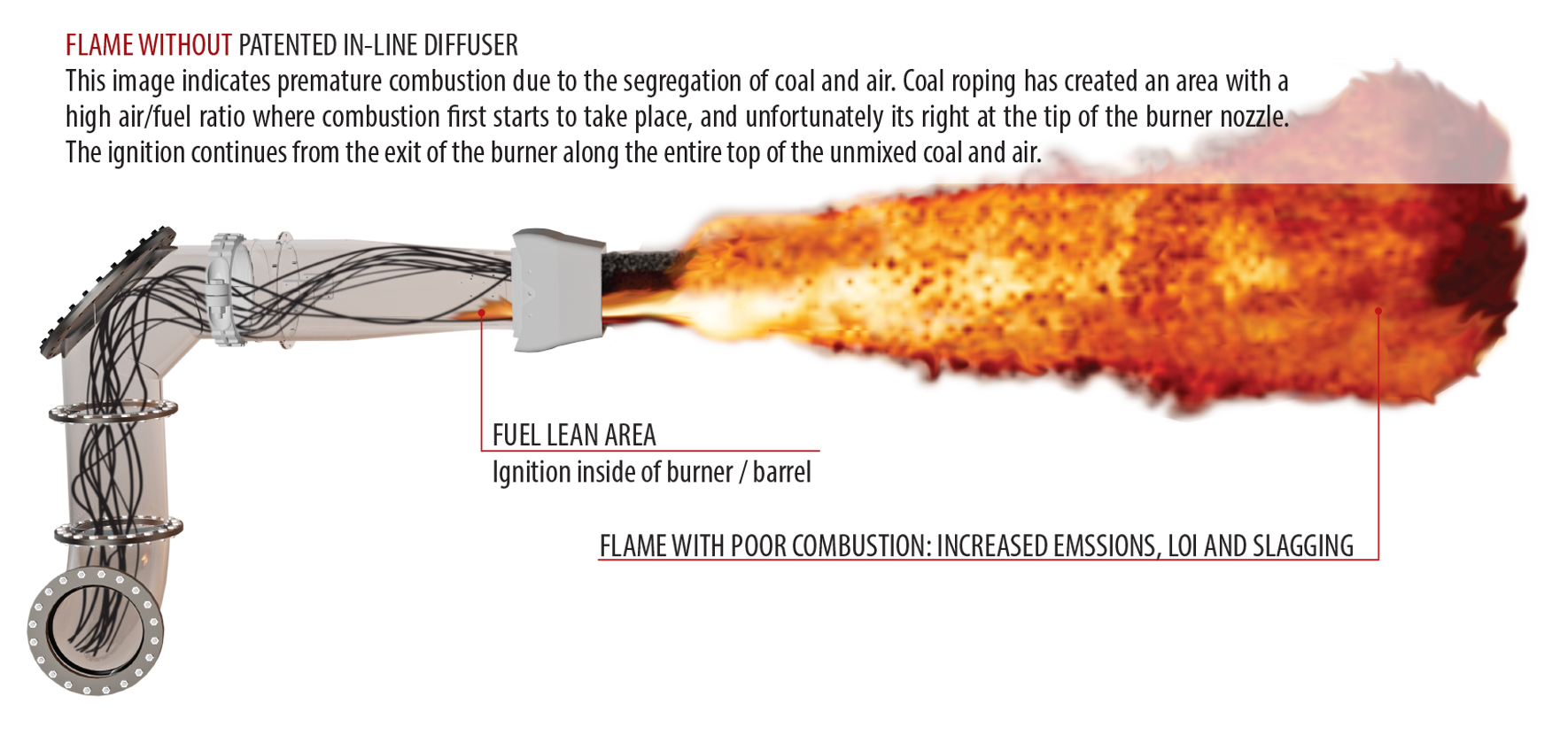
Corner-Fired Burners – Without Diffuser:
- Premature ignition at burner tip
- NOx spikes
- Risk of thermal damage to nozzles
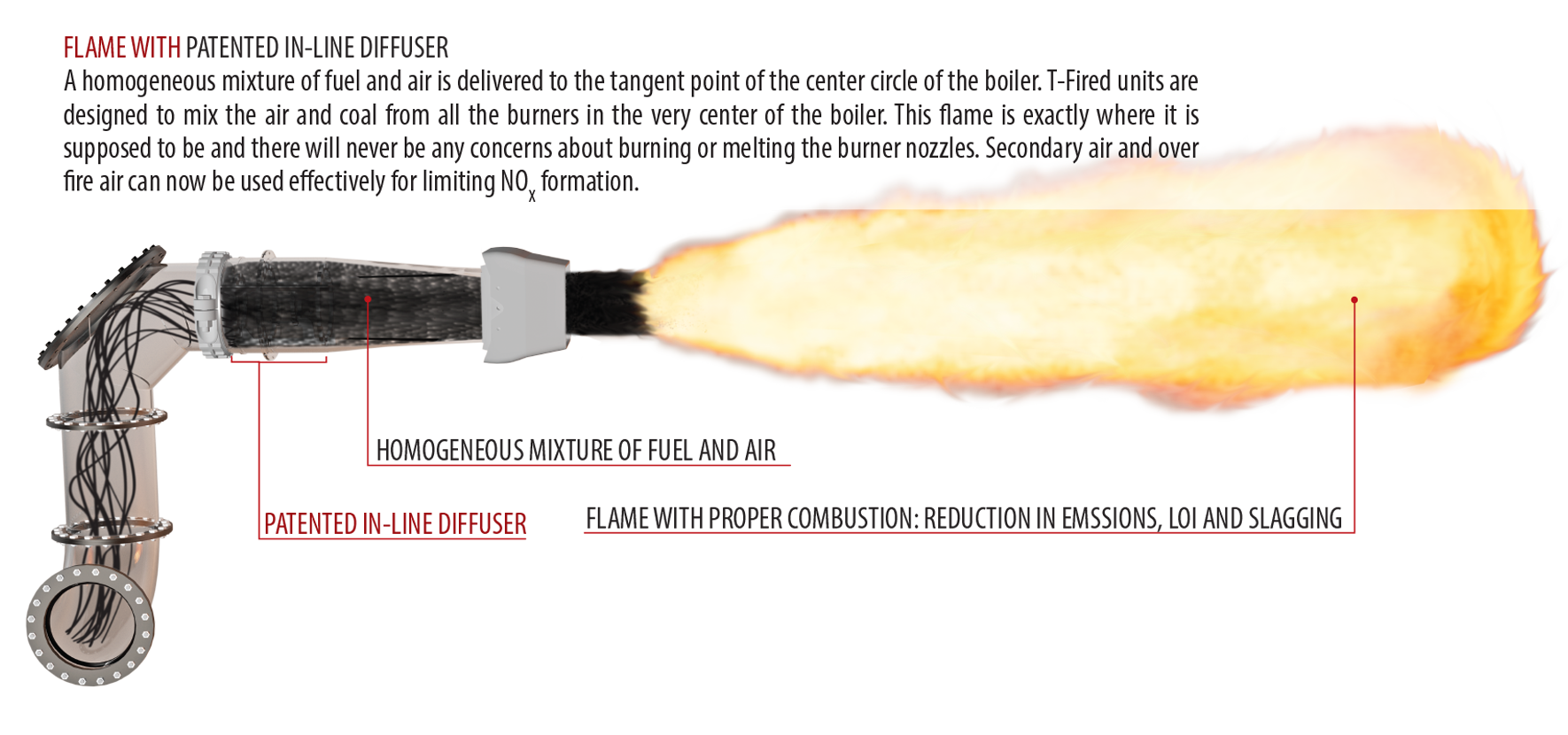
Corner-Fired Burners – With Diffuser:
- Combustion occurs exactly as design
- Homogeneous mix delivers a controlled, complete burn
- Burners last longer, NOx levels drop
Real-World Results: A Case Study Worth $150,000
A 600 MW coal-fired plant using 50 Riley Low NOx burners encountered serious issues after switching to a mid-sulfur coal:
- Excessively hot burners
- Persistent high NOx emissions
- Flame imbalance
- Poor SCR efficiency
After multiple unsuccessful interventions, SAS Global’s In-Line Diffusers were installed in 40 burners. The results were dramatic:
- Eliminated hot burners entirely
- Improved flame consistency and burner reliability
- Reduced NOx emissions by 15%
- Saved $150,000 in SCR operating costs in just 5 months
That’s not just better combustion—it’s bottom-line impact.
BENEFIT | IMPACT |
---|---|
NOx Emissions Down 15% | $300,000+ annual SCR savings (based on 600MW unit) |
Reduced Burner Wear | Reduced replacement and maintenance costs |
Reduction in Slagging and LOI | Less boiler cleaning, fewer forced outages |
Improved Combustion Efficiency | better heat rate, improved dispatch competitivness |
Increased Flame Control | Enables true low NOx performance |
Typical ROI Payback Period:
< 12 months for most units over 300 MW with baseline NOx control systems in place.
Engineers and Plant Managers: It's Time to Rethink Your Burner Performance
If your Low NOx burner strategy hasn’t yielded the results promised on paper, it’s likely due to invisible inefficiencies—like coal ribboning. The SAS Patented In-Line Diffuser is a field-proven, ROI-positive burner modernization that ensures your burners work with your fuel system, not against it.
The science is sound. The results are proven. The flames don’t lie.
Want to See It in Action?
SAS Global has burner video footage showing combustion quality before and after diffuser installation. Request access or schedule a technical consultation to learn more.
View More on the SAS Patented In-Line Diffuser →
The In-Line Diffuser isn’t just another add-on; it’s a key to unlocking true low NOx performance.
Let’s burn smarter.