Modernize Your Airjet Burner Barrels: A Proven Path to Longer Life and Lower Costs
Why settle for outdated burner barrel technology when failure isn’t just inconvenient, it’s costly?
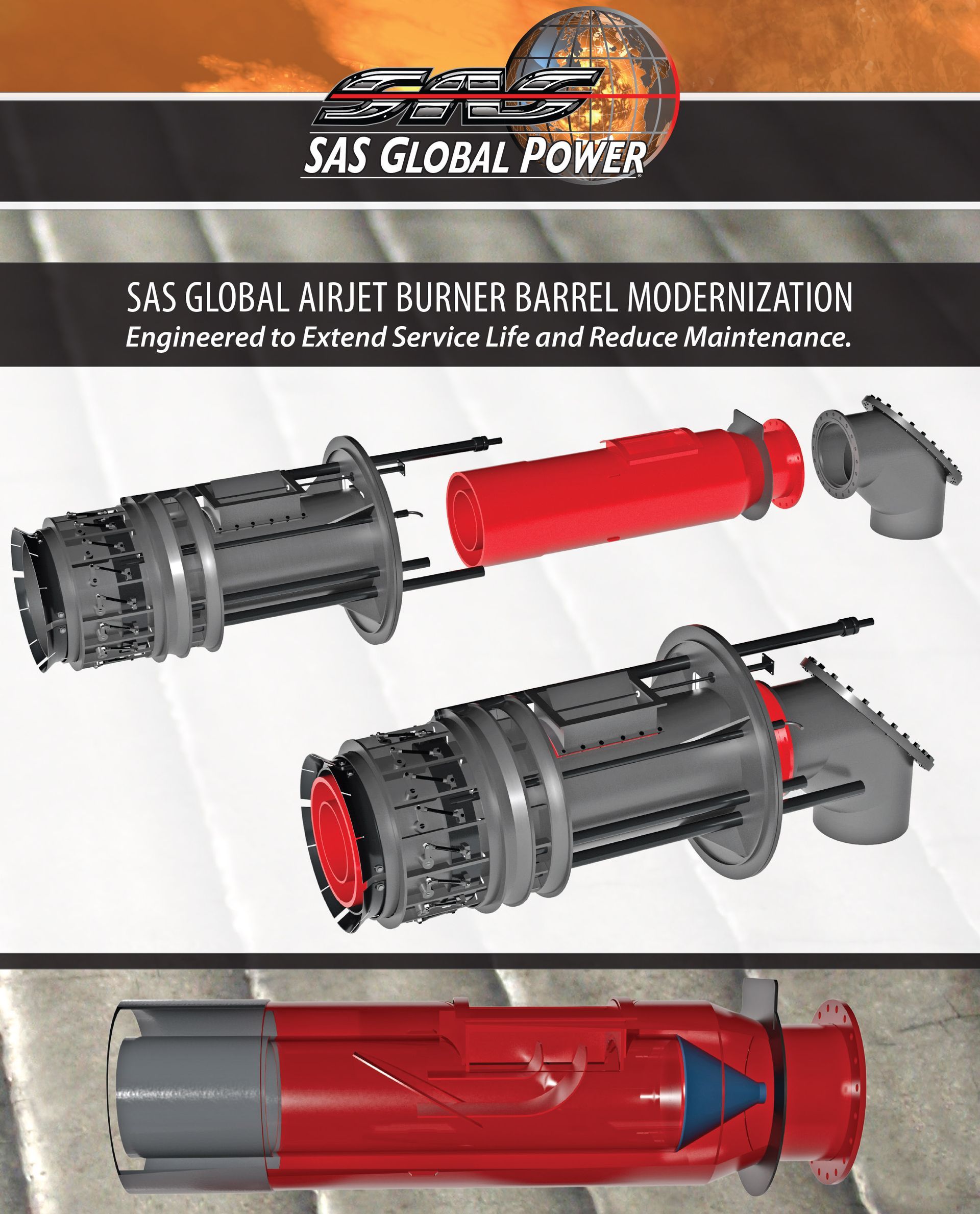
At SAS Global Corporation, we’ve spent over 70 years engineering wear and heat resistant solutions specifically for the demands of coal-fired power plants. Our latest innovation, the SAS Airjet Burner Barrel Modernization Program, delivers measurable performance improvements and long-term savings for operations that refuse to compromise on reliability or uptime.
The Problem with Legacy Designs
OEM burner barrels, whether
ceramic-lined or
fabricated stainless steel,
have common failure points:
- Warped nozzles under high thermal cycling
- Tile delamination or cracking, especially under cold starts
- Frequent replacements, increasing maintenance downtime
- Inconsistent combustion performance and slagging
SAS Has the Solution: Engineered Resilience Meets Practical ROI
SAS Airjet Burner Barrels are engineered from the ground up to solve those pain points. Designed as
drop-in retrofits, our barrels integrate premium materials and intelligent fabrication to deliver:
Key Engineering Advantages – Designed for Real-World Power Plant Demands
1. No Tip Warping or Thermal Distortion
Problem:
Legacy burner barrels made from thin stainless, layered alloy steel, and/or ceramic-lined structures that often suffer from tip deformation due to repeated thermal cycling and sustained exposure to high temperatures during operation.
SAS Solution:
SAS fabricates the
front 20" nozzle section from
1" thick Spuncast HN Stainless Steel, a high-nickel alloy engineered specifically for high-temperature resilience.
Engineering Benefit:
- Maintains geometric integrity under extreme heat
- Prevents hot spots and air pattern distortion at the burner tip
- Eliminates the need for frequent inspections or realignments
- Supports uniform flame shaping and better combustion profiles
2. No Tile Debonding, Cracking, or Delamination
Problem:
Traditional ceramic-lined barrels degrade over time—tiles crack, shift, or fall off due to thermal expansion mismatch, cycling stress, or poor adhesive retention.
SAS Solution:
We’ve replaced the failure-prone tile system with a monolithic
SA6000® Inlet Deflector Cone, made of a proprietary composite overlay specifically designed for high-wear, high-temp airflow regions.
Engineering Benefit:
- No adhesives or layered construction to fail
- No downstream FOD (foreign object debris) from failed tiles
- Enhanced safety and operational consistency
- Reduced inspection frequency and outage risk
3. Thermal Shock Resilience
Problem:
Coal-fired units, especially cycling plants or peaking assets, face significant temperature fluctuations from startup, ramp-up, and load swings. These shocks often lead to premature failure in OEM designs.
SAS Solution:
Our barrels are built using
SureAlloy® premium carbide overlays,
Spuncast stainless steel, and
precision-engineered joints to absorb and survive repeated thermal expansion/contraction cycles.
Engineering Benefit:
- Withstands rapid thermal ramp-ups without cracking
- Ideal for units that cold start, two-shift, or cycle frequently
- Enhances structural reliability in multi-fuel and biomass co-firing units
- Extends barrel longevity even in high-slag or high-ash environments
4. Optimized Combustion Performance and Airflow
Problem:
Inconsistent air-to-fuel ratios at the burner can lead to poor flame control, carbon carryover, increased slagging, and emissions non-compliance.
SAS Solution:
SAS barrels can be designed with an integrated SAS Patented In-Line Diffuser, which promotes
uniform fuel and air distribution throughout the combustion zone.
Engineering Benefit:
- More stable flames and improved heat rate
- Reduced CO and NOₓ formation
- Lower risk of clinker formation and slagging
- Enhances downstream heat transfer and tube integrity
5. Simplified Maintenance and Serviceability
Problem:
Time-consuming, labor-intensive repairs and inspections of legacy designs increase outage duration and labor costs.
SAS Solution:
Our burner barrel assemblies are designed as
ready-to-install drop-in retrofits, compatible with existing burner throat geometry and support brackets. All designs are fully QA/QC verified to ensure fit-up and thermal alignment.
Engineering Benefit:
- Faster installations during outages
- Reduced man-hours and safety risk
- Better inspection visibility and access
- Minimizes scheduled and unscheduled downtime
What You Get with an SAS Upgrade
- Extended service intervals and lower lifecycle cost
- Elimination of tile-based failure mechanisms
- Reduced slag buildsp and more uniform combustion
- Simplified inspections and faster changeouts
- Fully QA/QC-verified designs, ISO-compliant
Complete System Modernization
In addition to barrel assemblies, SAS Global also engineers and fabricates:
- Inlet Elbows (Flatback and Turtleback)
- Fuel Piping Systems
- Custom SureAlloy® Wear Packages
Each is available in a range of premium carbide overlay materials to match your exact fuel, ash content, and wear environment.
Ready to Upgrade? Let’s Talk.
Don’t wait for another failure.
Upgrade now to eliminate the chronic costs of legacy burner barrels.
Contact SAS Global Corporation
info@sasglobalcorp.com |
www.sasglobalcorp.com
ISO-Certified | Made in the USA | Power Industry Trusted
Stop replacing the same failed parts.
Start investing in reliability engineered to last.
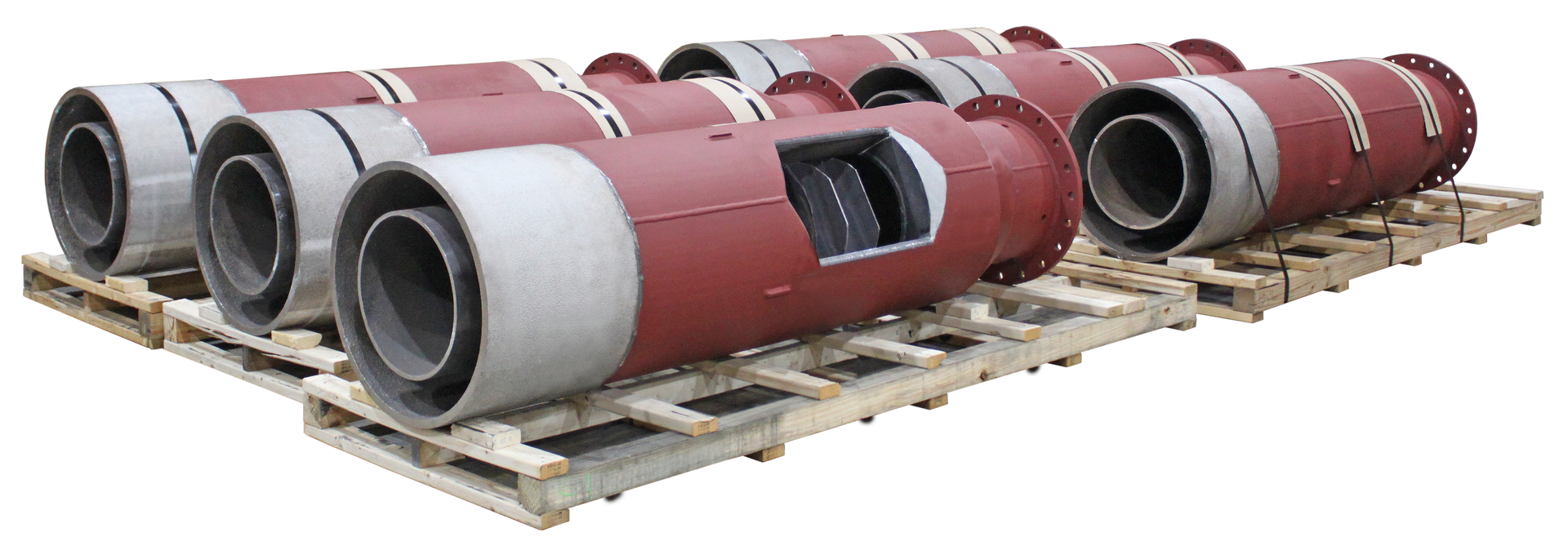